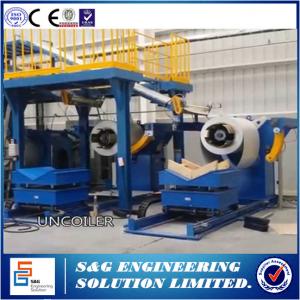
Add to Cart
60 KW Power Double Belt Discontinuous PU Sandwich Panel Production Line with 700 ~ 1000 Width For PU Sandwich Panel
Details of Roll Forming Machines
This machine is suitable to PU sandwich production, such as wall panel and roofing panel.
The plate can insulate heat, sound, and prevent burn, widely used in roof panel, wall panel, and so on.
Main Roller Forming Machines--------------Two SETS
1: Coil width: 1220/1100mm effective width: 1000mm
2: working speed: 12-15m/min (not contain cutting)
3: roll station: 20/13 stations
4: material of roller: grade 45 steel, polished and coated with chrome
5:material of main shaft:45﹟ steel diameter roller: Ф70mm
6: main power: 5.5KW
7: forming thickness: 0.3mm—0.8mm zinc and color steel, G250MPA
8: Transmission: by single Chains 1.0 inch
9: feeding and guide: surface polished and coated with chrome
10: machine drive parts adopt protect cover
11: machine adopt new station with chrome
12: size of main machine: max 8000x1300x1200(mm) L x W x H
13: weight: about 5500Kgs
14: color of machine: blue (also can choose by customer request)
15: machine should be with four legs (made from metal) in 350mm
Uncoiler For Material Feeding --------------Two SETS
Ⅱ. PU Insulation Part
Specifications of sandwich panels producible:
Max. length 6000mm
Max width 1000mm
Thickness 30mm
Equipment used:
1. One “1+1” double-layer laminator for steel Panel
2. One set of PU foaming injection machine
Operating principle:
The sandwich panel consists of double layer CORRUGATED panel,the foam will be between these panels.
The double-layered laminator is consisted of the press and the rail stands.Initially, put the top and the bottom facing sheets inside of mould frames and then do the necessary sealing work. After that, feed the worktables into the press. When worktables inside the press moves out orderly, the other two feed in at the same time. Upon the finish of feeding, the press will close and slant at a angle, waiting for the injection PU raw materials from the PU mixing head into different panels. Meanwhile materials start foaming and curing. At this time, mould frames on worktables moved out can be opened and the finished products can be unloaded to get ready for next production cycle.
Constituents of Equipment:
One “1+1” double-layer laminator for CORRUGATED panel:
The laminator is used to make sandwich panels with the max. lenth of 6m, max. width of 1.0m and the thickness 30mm.
1. Main technical parameters
Thickness of sandwich panel 30mm
Max bearing force 0.2Mpa/cm2
Moving speed of worktable 15-20m/min
Pressing speed 10~30mm/s
Working temperature of worktable 0~50℃
2. Main machine
To be made up of the frame, chassis, slanting mechanism, rails and beam.
2. 1 Worktable
Worktables are made of extruded aluminum alloy.
worktable (is fixed),manual-feeding ,and mould locators are provided.
2. 2 Worktable heating system
It is made up of the medium heating installation, pump units, pipes and suitable temperature control. (Two sets, one on the right, the other on the left)
2. 3 Electric control system
Adopting central control by a panel, the system is equipped with fitting press buttons, relays, temperature control instrument, etc..
Hi-pressure PU foaming machine
Tank assembly:
Producing tank: Two 300L , maximum allowable pressure 0.4MPa. Each tank is with a 0.75kw agitator assembly and the safety valve, pressure-reducing valve, pressure gauge, three-position liquid-level control switch and fitting valves and pipes.
Automatic material-supplementing installation: two material-loading tanks included; material loading done either in an automatic or a manual way.
Material filtration part includes two wire-type filters.
Material | Raw material | colored steel plate, galvanized plate, or aluminum plate |
Thickness | 0.3-0.8 mm (As customer`s need) | |
Feeding width | 300mm-1250mm (According to customer`s profile) | |
Material hardness: | 550 Mpa---350 Mpa | |
Hydraulic Uncoiler | Inner Diameter | 510-610mm |
Max Coil width | 1250mm | |
Capacity | 10T/8T | |
Hydraulic cylinder lift stroke | Up panel 0.5m, Down panel 0.5m | |
Coil car stroke | 2.5m | |
Pressure of hydraulic system | 6.3Mpa | |
Main Forming | Forming steps | 24 stations ( Depend on Profiles ) |
Shaft diameter | Φ60mm | |
Design type | Middle plate welded | |
Transmission | Gear box (Chain and gear box depend on thickness and customer`s need) | |
Machine frame | 350# H steel welded; Steel plate welded/ Memorial arch frame type | |
Roller material | Gcr15MoV | |
Shaft material | 45# steel with tempering | |
Cutting blade material | Gcr12MoV quenched | |
Working speed | 12-15m/min | |
Power of machine | 60KW (According to the thickness) | |
Type of cutting | Hydraulic | |
Cutting tolerance | ±1mm | |
Material of blades | Gcr12 quenched | |
Cutter quantity | 1 set | |
Working pressure | 20MPA | |
Pre-heating Room | Temperature sensor | Hot couple |
Temperature adjustment | Automatic control by temperature control equipment | |
Hot air motor | 18.5Kw | |
Hot air heater | 200Kw | |
Heat type | Heated by electricity and air circulate | |
Flying Saw Cutting Machine | Outline dimension of band saw cutting machine | 5500mmx5000mmx 3000mm |
Run speed of band saw | 1000-1500rpm | |
Rotate diameter of band saw | 550mm | |
Cutting speed of band saw | 50m/min-1000m/min | |
Width of band saw | 30mm | |
Length of band saw | 3000mm-4000mm | |
Transverse move distance | 1500mm | |
Cut length on line | 3000mm | |
Configurations | Uncoiling→ (Perforation machine )→Feeding material into machine→ Roll forming→ PU foaming→ Pre-heating Room→ Auto cutting→ Products receiving | |
![]() |
Other Spare part | Weight | About 25 ton |
Dimension | 42000mm * 3600mm * 3300mm | |
Main body color | As required | |
Voltage | 380v/50hz/3ph(or as required) | |
Suitable working temperature | About 25℃ | |
Spare cutting blade | One piece | |
Fuse | 2 pieces | |
Relay | 2 pieces | |
Travel switch | 2 pieces | |
Solenoid valve | 1 pieces |
Applications:
With a wide range of different colors, available in cut-to-length supply and ready-to-install,
this modern building product takes a good share in a highly economic, weather-independent and fast,modular building process.
Beside the extremely high thermal-insulation values of the polyurethane-core,the panels create
a high overall stiffness with their "composite" function and therefore support very good statically values.
Advantages :
• Light weight: 10~ 14 kg/m2and hence reduced steel frameworks and system can become economical.
• Good thermal insulation, with average coefficient of thermal conductivity is 0.018 ~ 0.020 W/mk.
• Available in customized length. And in wide range of colors.
• Cold and heat resistance: Perfect temperature resistance deformation from -110º C to 120º C.
• Great energy saver and hence indispensable in air-conditioned, cooled and heated buildings.
• Virtually zero maintenance throughout life.
• Installation is convenient and Flexible; not requiring large- scale lifting devices, and thus lowering building costs.
• High intensity and large rigidity ensures suitability for weight-bearing structures and for supporting and protective structures.
• Non-water absorbent.
• Environmentally friendly. And bring down life cycle cost for any built environment.
Our Services and Terms:
Terms of Payment: 30% of the total contract value paid by T/T as down payment, the rest 70% of the total contract value to be paid by T/T after inspection by buyer in seller’s factory while before delivery.
Delivery: 100 days after receipt of advance payment
Service: we send technician to your country to install the machine.The buyer should take all the cost including: visa, roundtrip tickets and suitable accommodation, also buyer should pay salary 80 USD/day.
Warranty: 12 months limited warranty
During warranty: parts are free but buyer pay for the shipping fee
Pu Sandwich Panel Picture:
Machine Picture: